Our Facilities
We provide our customers with cost-effective in-house design and engineering. Product development includes acoustic modelling analysis, mechanical and electrical design, prototype build and evaluation, through to the final product manufacture to deliver the best acoustic product solution. With all the facilities on one site, we can transform a customer specification or idea into a fully working solution.
Engineering Design

Acoustic Design & Modelling
Utiliising a combination of analytical models and finite element modelling the team can design new transducer elements and arrays to meet the most demanding of applications.
Mechanical Design
A qualified team of mechanical design engineers utilise the latest version of SolidWorks to assist them in producing the most imaginative ideas, the team also use PDM to control and maintain drawings and documents from product development to production documentation.
Electronics Design
Consisting of qualified electronics hardware and software engineers responsible for the design and integration of front-end electronics for our sonar transducers and arrays.
Manufacturing Facilities
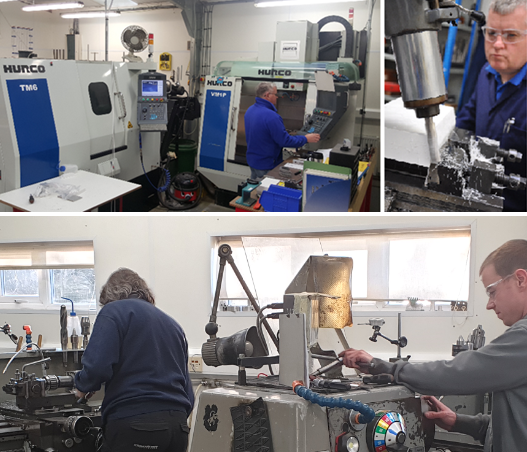
Machine Shop & Engineering Tool Room
With both conventional machines as well as the latest Hurco CNC machines, our qualified tool-makers and machinists are capable of making mould-tools, jigs & fixtures, one-off prototypes to large batch production quantities.
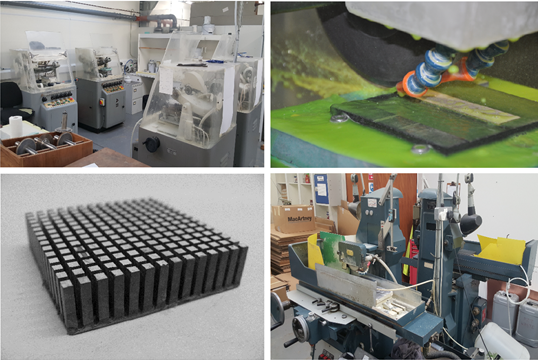
1-3 Piezo-Composite Machining
Consisting of four PZT ceramic automatic slicing machinings, two surface grinders, and two universal grinders, for processing solid PZT ceramic into 1-3 PZT composite shapes.

Monolithic & 1-3 Piezo Composite Assembly
Neptune have produced monolithic and 1-3 PZT transducers for 30 years, these typically include tonpilz elements, linear ceramic arrays, pre-stressed free-flooded rings and spherical ceramic transducers for active broadband projectors and passive hydrophones.

Moulding & Encapsulation
The majority of Neptune's products are encapsulated in polyurethane designed especially for the underwater sonar industry. We use several different materials depending on the application, either optimising acoustic matching or providing mechanical, shock and environmental protection. We have also developed our unique materials for acoustic backing to give good decoupling over large frequency ranges. All the materials are designed to have low viscosity to reduce air entrapment and thus allowing the encapsulation of complex parts.

Acoustic Calibration & Testing
With the largest privately owned laboratory of its type in the UK, it is equipped with the most technically advanced instrumentation and software, providing engineers and scientists with the ability to perform accurate underwater measurements on a wide range of underwater acoustic equipment. Available to hire, manufacturers and end-users alike will find the facility invaluable whether calibrating a single hydrophone or establishing the underwater performance of a complex sonar system. All measurements are traceable to national standards.