Piezo Composite Technology
Neptune Sonar have a long history of producing reliable and cost effective transducer designs and can offer further design flexibility with the addition of piezo-composite technology to our existing manufacturing capabilities, through our Zeus Piezoceramics venture.
Piezo-composite is a modified form of standard PZT where diced ceramic pillars are encapsulated into a polymer matrix to form a homogenised acoustic material with adjustable properties. These materials are inherently broadband with good sensitivity and acoustic coupling efficiencies.
The unique properties of composites offer greater range in transducer performance and can be readily formed into 3 dimensional shapes.
Neptune Sonar uses the dice and fill technique in the manufacture of composite ceramic. This provides the ability to optimise ceramic geometry to best suit the application.
BACKGROUND


Amplitude Gain
The accumulation of lateral displacement within solid ceramic (d31) restricts the amplitude in the thickness mode (d33). Conversely in 1-3 composite the relatively small lateral displacements can to be taken up within the compliant polymer matrix surrounding each pillar. Hence there is more displacement energy available in the thickness mode.
Sensitivity Gain
By reducing the area of ceramic for a given aperture (volume fraction) it is possible to increase the strain energy within each pillar compared to its solid ceramic counterpart. The less ceramic and the more compliant the matrix material is, more strain energy is exerted on the pillars. Gains in excess of 5dB are not uncommon.
Transducer Characteristic Comparison
Unwanted frequency modes can be reduced to near zero values in composites by the internal damping properties of the polymer matrix. The multiple resonant frequencies that are normally seen in monolithic ceramic require electrical and/or acoustic filtering to achieve equivalent performances.
For linear and curved phased arrays, particularly, there are advantages that can be gained to offset the additional manufacturing costs of composite. Principally, there is improved electro-acoustic uniformity with less crosstalk between channels and a reduction in the number of individual components per transducer array.
Transmission Efficiency Gain
Due to the reduction in ceramic content within the composite, the resultant acoustic impedance is more closely matched to that of water at 1.5 Mrayl. Hence there are less internal reflection losses than in solid ceramic (assuming no matching layers.)
PROCESS
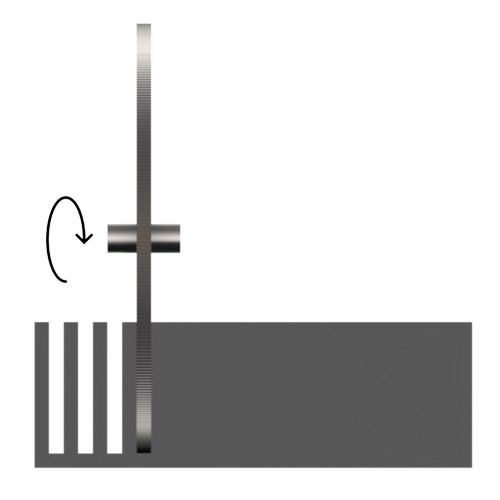




SUMMARY
Advantages
- Unimodal frequency response across operational band – Design simplicity
- Frequency independent stave geometry – Aperture design flexibility
- Improved curved array performance – Smooth radius of curvature
- High sensitivity / high pulse amplitude – Good signal to noise ratio
- Broad bandwidth – Q = 4 to 5 (typical)
- Increased range resolution – Short pulse lengths possible
- Improved phase uniformity at resonance – Good angular resolution
- Improved coupling efficiency – Good acoustic match to water
- Readily formed into 3 dimensional shapes – eg Cylindrical and spherical
Disadvantages
- Reduction in capacitance – Percentage loss of ceramic area
- Higher manufacturing costs – More processing required
- Thermally insulating – Power and duty cycle limited
- Performance compromises at higher depth rating – Material compliance issues
TYPES OF 1-3 COMPOSITE



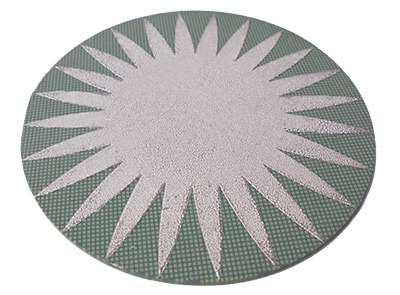